Sand hole (sand hole)
Features: relatively regular holes are formed on the surface or inside of the casting, and their shape is consistent with the shape of the sand particles. When the mold is just pulled out, the sand particles embedded on the surface of the casting can be seen, from which the sand particles can be taken out. When multiple sand holes exist at the same time, the surface of the casting is orange peel.
Cause of formation: holes are formed because the sand particles falling from the surface of the sand core are wrapped with the casting surface by liquid copper.
- The surface strength of the sand core is poor, scorched, or not completely cured.
- The size of the sand core is inconsistent with the external mold, and the sand core is crushed when closing the mold.
- The mold was dipped in graphite water contaminated with sand.
- The sand falling from the friction between the ladle and the sand core at the sprue rushes into the mold cavity with the copper water.
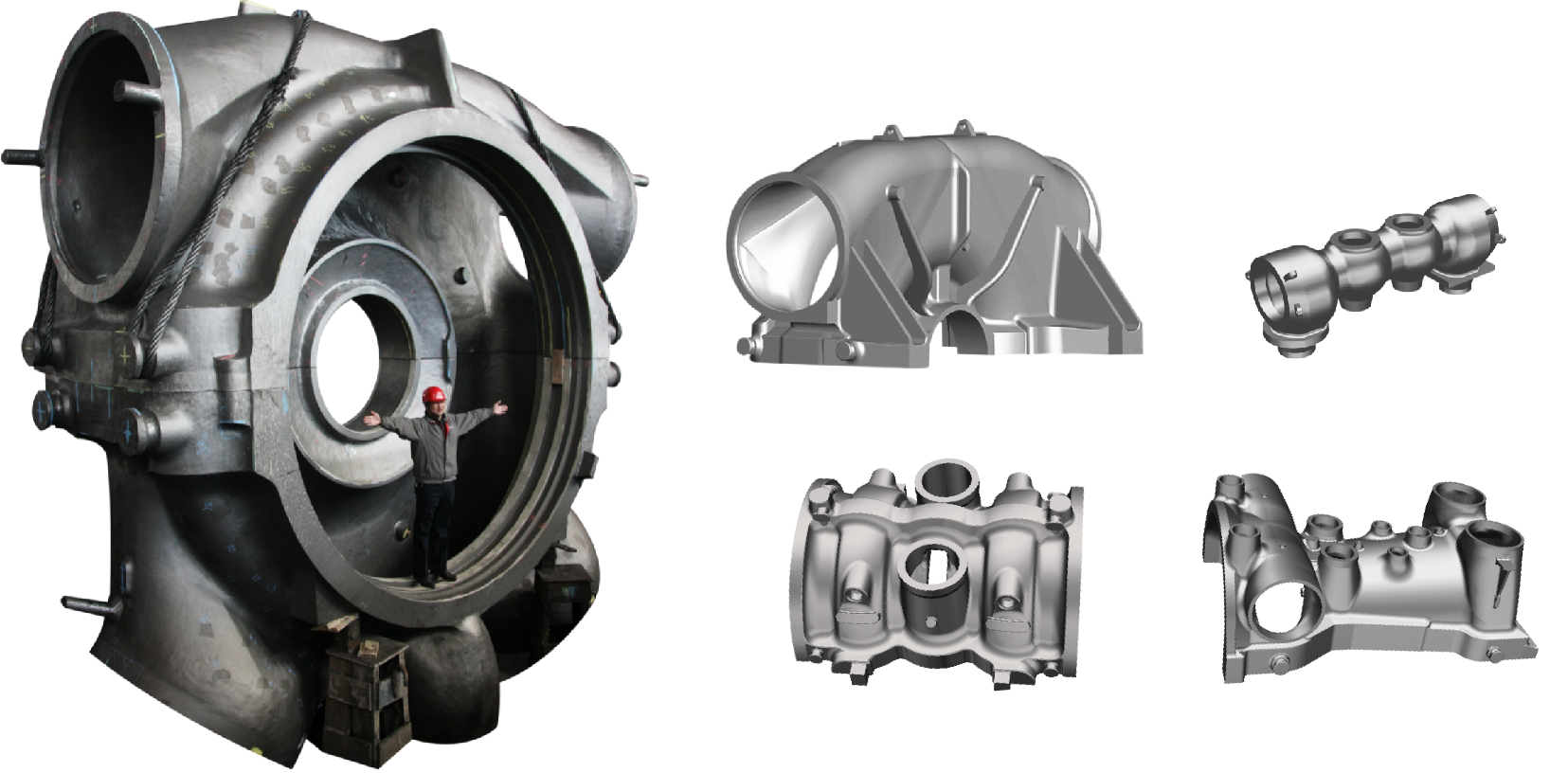
Prevention methods:
- The sand core shall be produced in strict accordance with the process and the quality shall be checked.
- The size of the sand core is consistent with that of the external mold.
- Graphite water should be cleaned in time.
- Avoid friction between ladle and sand core.
- The sand in the mold cavity should be blown clean when lowering the sand core.
Air hole (bubble, choke hole, air pocket)
Features: pores are holes on the surface or inside of castings, which are round, oval, or irregular. Sometimes multiple pores form an air mass, and the subcutaneous skin is generally pear-shaped. The choke hole has an irregular shape and rough surface. The air pocket is a concave piece on the surface of the casting, and the surface is smooth. Open hole appearance inspection can be found, and subcutaneous pores can be found only after machining.
Cause:
- The preheating temperature of the mold is too low, and the liquid metal cools too fast when passing through the gating system.
- The mold exhaust design is poor, and the gas cannot be discharged smoothly.
- The coating is not good, its exhaust performance is poor, and even volatilizes or decomposes gas.
- There are holes and pits on the surface of the mold cavity. After the liquid metal is injected, the gas in the holes and pits expands rapidly and compresses the liquid metal, forming choke holes.
- The surface of the mold cavity is rusted and not cleaned up.
- Raw materials (sand cores) are stored improperly and not preheated before use.
- Poor deoxidizer, insufficient dosage or improper operation, etc.
Prevention method:
- The mold should be fully preheated, the particle size of the coating (graphite) should not be too fine, and the permeability should be good.
- Pour by tilting.
- Raw materials should be stored in a ventilated and dry place and preheated during use.
- Choose a deoxidizer (magnesium) with a better deoxidation effect.
- The pouring temperature should not be too high.
Shrinkage cavity (shrinkage porosity)
Features: shrinkage cavity is a kind of hole with a rough surface on the surface or inside of the casting. A slight shrinkage cavity is many scattered small shrinkage cavities, namely shrinkage porosity, and the grain at the shrinkage cavity or shrinkage porosity is coarse. It often occurs near the inner sprue of the casting, at the root of the riser, at the thick part, at the thickness transition of the wall, and at the thickness of the large plane.
Cause:
- The mold working temperature control did not meet the requirements of directional solidification.
- Improper coating selection and poor control of coating layer thickness at different parts.
- The position of the casting in the mold is not designed properly.
- The design of pouring and riser fails to play the role of full feeding.
- Pouring temperature is too low or too high.
Prevention methods:
- Increase the temperature of abrasive tools.
- Adjust the thickness of the coating layer, spray the coating evenly, and do not form local coating accumulation when the coating falls off and is repaired.
- The mold is locally heated or partially insulated with insulating materials.
- The hot spot is inlaid with copper blocks to chill the local part.
- Heat sinks are designed on the mold, or the cooling speed in local areas is accelerated by water, or water spray and spray are sprayed outside the mold.
- The demountable chilling block is used and placed in the mold cavity, in turn, to avoid insufficient cooling of the chilling block itself during continuous production.
- A pressurizing device is designed on the mold riser.
- The design of the pouring system should be accurate and the appropriate pouring temperature should be selected.
Searching for a casting part design, components of casting, bearing housing casting supplier, wholesaler, manufacturer from China, you can get high-quality products at a nice price.